Sawdust pellet machines play a vital role in transforming wood waste into high-density pellets used for energy generation, animal bedding, and various other applications. To ensure optimal performance, efficiency, and longevity, regular inspection and maintenance of the machine’s components are essential. Knowing when to perform these inspections can help avoid costly downtime and maintain consistent production quality. This article outlines the key components of a sawdust pellet machine that require regular checks and the best timing for these inspections.
1. Pellet Die
The pellet die is one of the most crucial components of a sawdust pellet machine, shaping raw materials into pellets.
- Inspection Frequency: Inspect the pellet die after every production cycle or daily, depending on production volume.
- Signs to Look For: Monitor for wear, such as enlarged holes, cracks, or uneven surfaces. A worn die can negatively impact pellet quality and increase energy consumption.
- Best Time for Inspection: Check the die at the end of each production day to detect wear that may have occurred during operation. Regular inspections can facilitate proactive replacements, minimizing production disruptions.
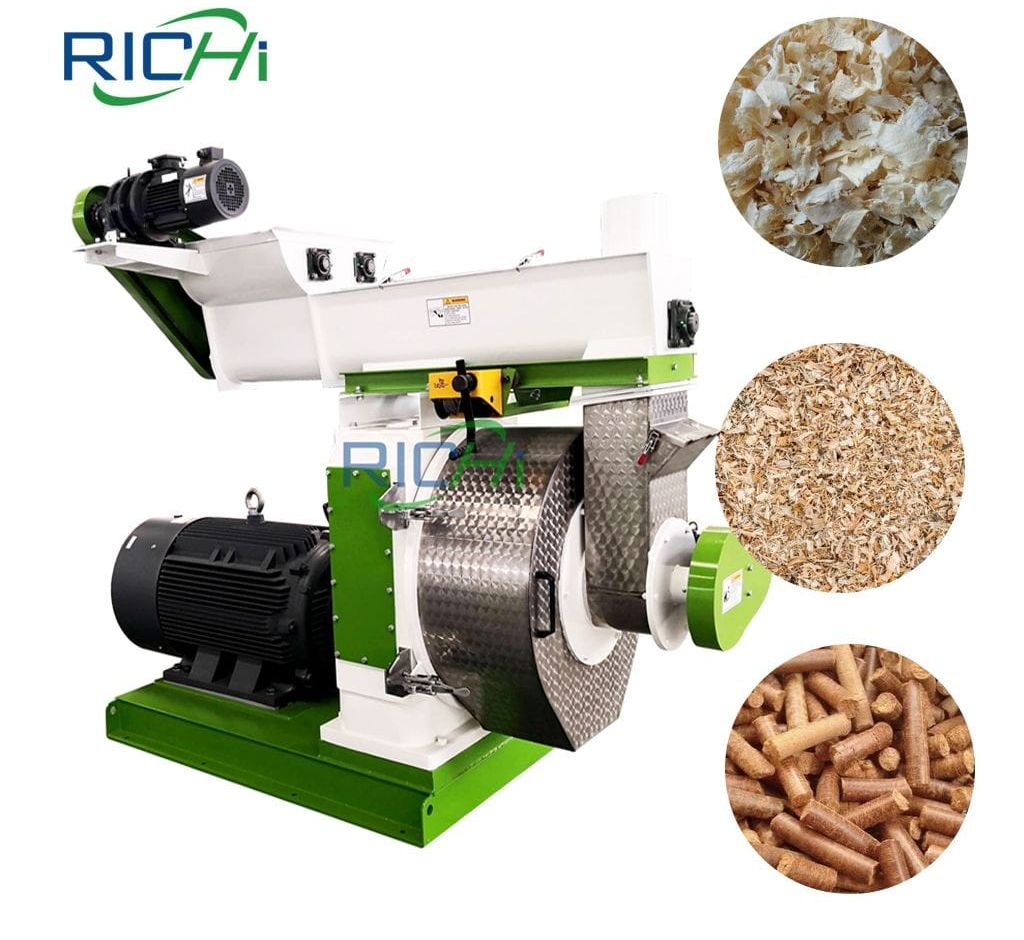
2. Rollers
Rollers work alongside the die to compress the sawdust material into pellets.
- Inspection Frequency: Inspect rollers weekly or after significant production runs.
- Signs to Look For: Look for uneven wear patterns, cracks, or excessive play in the roller shafts. Worn rollers can lead to slippage and inconsistent pellet quality.
- Best Time for Inspection: Conduct roller inspections during routine maintenance checks, typically scheduled weekly or bi-weekly. This timing allows for addressing any issues before they affect production efficiency.
3. Bearings
Bearings support the rotating components of the sawdust pellet machine, such as the roller and die shafts.
- Inspection Frequency: Inspect bearings monthly or during routine maintenance.
- Signs to Look For: Listen for unusual noises, vibrations, or excessive play in the shafts, which can indicate bearing wear. Check for grease leakage or overheating signs.
- Best Time for Inspection: Perform bearing inspections during the monthly maintenance schedule. Additionally, inspect bearings after extended periods of operation or when unusual noises are detected.
4. Gearbox
The gearbox transmits power from the motor to the pellet mill, ensuring that the appropriate speed and torque are applied during the pelleting process.
- Inspection Frequency: Inspect the gearbox monthly or during routine maintenance.
- Signs to Look For: Check for oil leaks, unusual noises, or vibrations that may indicate wear or damage to gears or bearings.
- Best Time for Inspection: Schedule gearbox inspections during monthly maintenance checks. Also, inspect the gearbox after any overload incidents or unusual operation to ensure proper functionality.
5. Lubrication System
The lubrication system is essential for providing adequate lubrication to various moving components of the sawdust pellet machine.
- Inspection Frequency: Inspect the lubrication system weekly to ensure proper functioning.
- Signs to Look For: Look for leaks, blockages, or insufficient lubrication levels. Inadequate lubrication can lead to excessive wear and potential damage to machine components.
- Best Time for Inspection: Conduct lubrication system inspections during weekly maintenance. Regular checks help ensure that all components are adequately lubricated and functioning smoothly. (Related post: wood chip pellet maker)
6. Feed Hopper
The feed hopper is where raw materials are loaded into the pellet machine and plays a critical role in regulating the flow of sawdust.
- Inspection Frequency: Inspect the feed hopper daily or before each production run.
- Signs to Look For: Check for wear or damage, such as cracks or blockages that could hinder material flow.
- Best Time for Inspection: Perform feed hopper inspections before starting each production day to ensure it is clean and ready for operation, facilitating a smooth feeding process.
7. Cooling System
Once the pellets are formed, they need to be cooled to maintain quality and prevent spoilage.
- Inspection Frequency: Inspect the cooling system weekly or during routine maintenance.
- Signs to Look For: Check for blockages, leaks, or inadequate cooling signs, such as soft or deformed pellets.
- Best Time for Inspection: Schedule cooling system inspections during weekly maintenance checks. Also, inspect the system after production runs resulting in unusually high pellet temperatures.
8. Electrical Components
Electrical components, including the motor, control panel, and wiring, are critical for the sawdust pellet machine’s operation.
- Inspection Frequency: Inspect electrical components monthly or during routine maintenance.
- Signs to Look For: Look for frayed wires, loose connections, or signs of overheating, such as discoloration or burning smells.
- Best Time for Inspection: Conduct electrical component inspections during monthly maintenance checks. Additionally, inspect these components after any electrical issues or malfunctions are detected.
9. General Maintenance Practices
Implementing general maintenance practices can enhance the overall performance and longevity of your sawdust pellet machine.
- Establish a Maintenance Schedule: Create a routine maintenance schedule that includes inspections, lubrication, and part replacements based on the manufacturer’s recommendations.
- Keep Records: Maintain detailed records of inspections, maintenance activities, and any issues encountered. This documentation can help identify trends and inform future maintenance decisions.
- Train Operators: Ensure operators are trained in proper machine operation and maintenance procedures. They should be able to identify potential issues and perform basic maintenance tasks.
Conclusion
Regular inspection and maintenance of the key components of a sawdust pellet machine are essential for ensuring optimal performance, consistent pellet quality, and minimizing downtime. By focusing on the pellet die, rollers, bearings, gearbox, lubrication system, feed hopper, cooling system, and electrical components, along with implementing general maintenance practices, you can help extend the lifespan of your machine and improve its efficiency.
Investing time and resources in regular inspections and maintenance will pay off in the long run by reducing operational costs, improving product quality, and enhancing the overall reliability of your sawdust pellet production process. As demand for renewable energy sources continues to grow, maintaining a well-functioning sawdust pellet machine will be crucial for success in this competitive industry.