A fertilizer pellet making machine is a molding machine that can make materials into specific shapes. The wet tooth fertilizer pellet making machine uses the mechanical stirring force of high-speed rotation and the resulting aerodynamic force to continuously realize the process of mixing, granulation, spheroidization, and densification of fine powder materials in the machine, so as to achieve the purpose of granulation.
This fertilizer pellet making machine granulation method makes the granulation rate higher, the granules are more beautiful, and at the same time saves energy and is highly energy-efficient.
1. Structural analysis of fertilizer pellet making machine
- The main structure of the fertilizer pellet making machine is an inclined rotating cylinder, and the drive can be constant speed or variable speed. When the liquid content of the feed powder is suitable, agglomeration occurs and tumbles in the drum.
- The drum has a certain slope, and the included angle between its axis and the horizontal is less than 10º, which can help the material to roll along the length of the drum, and a baffle ring is often installed at the feeding end to prevent the material from flowing back.
- A retaining ring can also be installed at the discharge end to increase the thickness of the material layer and prolong the residence time in the main drum. Sometimes the cylindrical screen is integrated with the rotating drum to form a product discharge port.
- The feeding of the fertilizer pellet making machine is composed of fresh material and circulating material, and the feeding system can adopt belt conveyor, chute pipeline or other similar equipment. The binding liquid is injected either before the solid material enters the rotary cylinder, or immediately after the solids enter the rotary cylinder.
- Like the disc fertilizer pellet making machine, the inner surface structure of the drum plays an important role in whether the material can react well in the drum. Inside the steel drum, general shirts have heat-expandable metal.
- The function of various internal scrapers is to maintain a certain thickness of the material on the inner surface of the drum, so that the material layer is uniform, and it is convenient for the material to roll and turn normally in the drum. Rubber baffles and liners as well as external shocks are used to prevent build-up during fertilizer granulation.
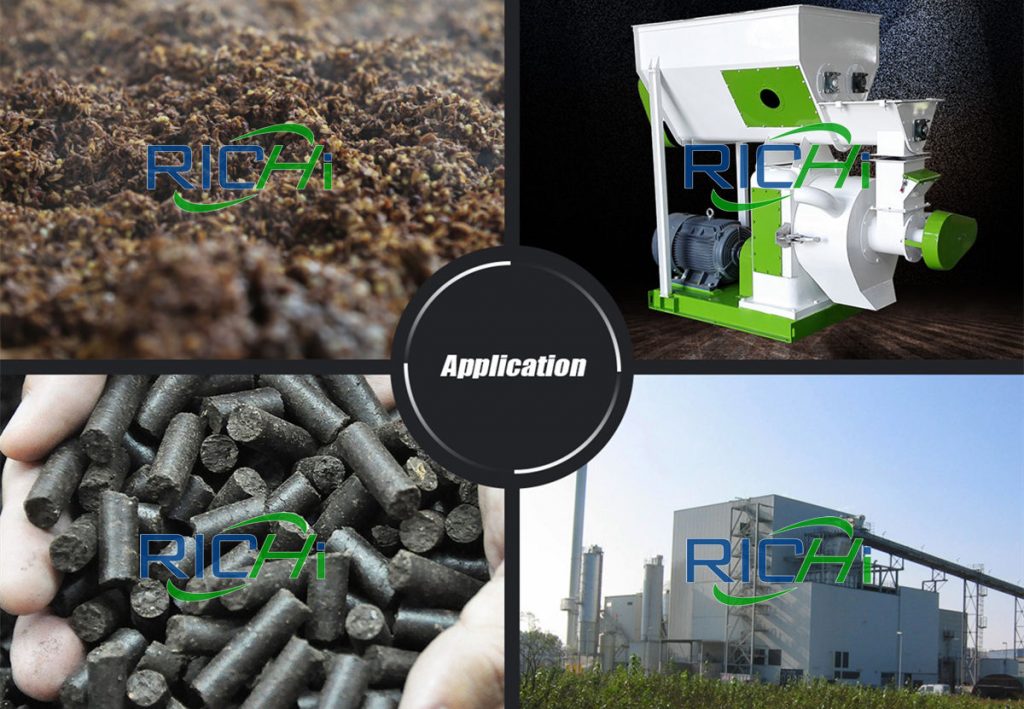
2. Moisture control of fertilizer pellet making machine
In the drum granulation, the coarsening of the pellets is mainly based on the cladding type, so the amount of material circulation should be larger, so this can provide a coarser core for the cladding process, and the water injection amount should be smaller, so that The water absorption of the core can be made less.
When granulating by bonding or “aggregation”, the material marriage is smaller than it should be because the material in the drum is mainly composed of fresh raw materials with small particle size and mutual bonding. The liquid ratio required for bonding should be large, because the gaps between the mutually bonded fine powder particles need to be filled with water.
Due to the deepening of the understanding of the granulation process, some suitable monitoring instruments have been developed, so that it is possible to simulate and automate the computer control of the granulation process.
3. Comparison of granulation systems
In order to make the right choice between the disc granulation system and the drum granulation system, a quantitative comparison of the two methods was made.
In the same workshop, when the fertilizer pellet making machine granulation process, process raw materials and monitoring conditions are the same, two processes are used for granulation at the same time, and the following conclusions are drawn from the comparison:
① The capital construction investment of the two fertilizer pellet making machine processes is roughly equal;
②The construction space of the disc granulation process is about 10% less;
③ The physical labor of the two processes is approximately equal;
④ The power consumption of the disc granulation system is high;
⑤ The noise of the disc granulation system is low;
⑥ The disc fertilizer pellet making machine needs less product and smaller equipment;
⑦ From the point of view of product quality, the two processes are not different.
From the perspective of the cost of granulation, combining the above four items, the disc granulation system is only 2% lower than the drum granulation system. Such a small difference prevents us from making a simple choice between the two.
According to the actual production needs, you can refer to the following methods to choose:
- The disc fertilizer pellet making machine has the characteristics of automatic classification, small footprint, low cost, zero operation, and easy observation. Therefore, it can be used to guide the granulation process for a wide variety of material types with precise agglomerates.
- Drum granulation has the characteristics of large production capacity, long logistics retention time, and multiple simultaneous processes. Therefore, it is suitable for the granulation of materials that are not easy to be granulated, and is suitable for mass production.
4. What does fertilizer pellet making machine line consist of?
(1) Turner
The function of this auxiliary equipment of fertilizer pellet making machine is to evenly toss the fermented material to make it fully contact with the air, dissipate a part of the water, and can crush the large material and the small material into powder, which has the function of a pulverizer.
(2) Forklift feeder
The function of this auxiliary equipment of fertilizer pellet making machine is to store the fermented materials and transport them to the next step evenly and quantitatively. The machine is equipped with a frequency converter, which can adjust the conveying speed of the belt conveyor.
The inside of the silo is equipped with an anti-smashing net, which can make the material slowly spill into the silo, and can separate large pieces of material. The middle and lower parts of the silo are equipped with an anti-blocking stirring device to prevent material blockage.
(3) New type chain pulverizer
The function of this auxiliary equipment of fertilizer pellet making machine can pulverize the fermented material into powder with more than 40 meshes, and it is better to control the moisture content of the material to less than 40%.
The Φ600 pulverizer can produce about 5 tons per hour, theφ800 pulverizer can produce about 7-8 tons per hour, and the φ1000 pulverizer can produce more than 10 tons per hour.
(4) Drum screening machine
The function of the machine is to screen the crushed materials, and the finished materials enter the next link. Due to the semi-wet material being screened, the mesh is easy to be blocked, and an anti-blocking and hitting device is generally installed. Screen out the large lumps or granules to see the ingredients for re-fermentation or discard.
With an annual output of 3000-5000 tons, a 1000*3000 screening machine is used, a 1200*4000 screening machine is used for the annual output of 10,000-20,000 tons, and a 1500*6000 screening machine is used for the annual output of 20,000-50,000 tons. A 100,000 tons of production use 2000*8000 screening machine, the mesh is 3-4 mm mesh, and the material moisture is less than 20% can use 1 mm screen, depending on the situation.
(5) Dynamic batching machine
The function of this auxiliary equipment of fertilizer pellet making machine is to mix several materials in strict accordance with the set ratio. The batching accuracy of this machine is 5‰.
(6) Double shaft mixer or single shaft mixer
These two kinds of equipment can play the role of continuous stirring belt transportation, which can fully stir the material evenly. The organic fertilizer mixer is mainly used for the mixing of raw materials, and the pan is lined with polypropylene plate or stainless steel plate, so it is not easy to stick the material.
Wear-resistant, the use of cycloidal pinwheel reducer has the characteristics of compact structure, convenient operation, uniform stirring, convenient discharging and conveying, etc. This auxiliary equipment of fertilizer pellet making machine is suitable for use in the production line of organic fertilizer equipment, and is lined with polypropylene plate or stainless steel plate.
Start the main stirring motor, drive the stirring parts to work through the sprocket deceleration drive, and according to the formula set by the electronic instrument, put various raw materials into the organic fertilizer mixer through the loader or manually, and the various raw materials are counted through the cooling system.
The materials are mixed, turned, sheared and rubbed in the mixer to achieve the purpose of fully mixing various raw materials and strains. Finally, the discharge motor drives the opening and closing of the material door to realize the discharge operation.
(7)Cache silo, the function of this auxiliary equipment of fertilizer pellet making machine is to store finished organic fertilizer materials, the machine is equipped with a frequency converter to adjust the speed of the conveyor.
It is possible to control the packaging scale with electrical appliances to convey materials when needed, and to stop conveying when not needed, ensuring that the powder packaging scale has flowing materials at any time without causing material blockage.
(8)Finished product packaging scale, the function of this auxiliary equipment of fertilizer pellet making machine is to quantitatively package finished materials (20-50 kg), with bucket (weigh the weight before the card bag, and directly drop the material after the card bag) and without bucket (blank the material after the card bag). Weighing) two models, there are bucket scales equipped with automatic hemming machine, automatic sewing machine, and automatic thread trimmer, which only needs one person to operate.
No bucket scale requires 2 people to operate. The double bucket packing scale is used for the production of more than 10 tons per hour. Automatic packaging into automatic operation state, when the controller receives the start information.
Then the bag clamping mechanism responds quickly, clamps the bag, delays for a period of time, the controller simultaneously opens the rapid feeding valve, the material falls into the bag, and the bag when the weight in the middle reaches the set value of fast feeding.
And the feeding speed will be switched to slow feeding to slow down the feeding speed and ensure the accuracy of weighing. When the material weight reaches the set value of slow feeding, close the slow feeding valve.
After a little delay, until the air material reaches the material bag, then open the bag clamping mechanism to complete the dynamic weighing process. The setting value of fast and slow feeding can be set by the user according to the fluidity and density of the material, as well as the user’s experience.
I hope the above related content about fertilizer pellet making machine is helpful to you. For more information about organic fertilizer pellet making machine, you are welcome to consult the staff of Richi Machinery, we will serve you wholeheartedly!