1. Introduction
In the production of organic fertilizers, high – moisture raw materials are commonly encountered. These raw materials, such as fresh manure, certain types of wet compost, and some industrial organic waste, pose significant challenges to the operation of organic fertilizer pelletizers. High – moisture content can lead to problems such as poor granulation, equipment clogging, and low production efficiency. To address these issues, it is necessary to develop targeted improvement schemes for organic fertilizer pelletizers. This article will comprehensively explore the improvement schemes for organic fertilizer pelletizers when dealing with high – moisture raw materials.
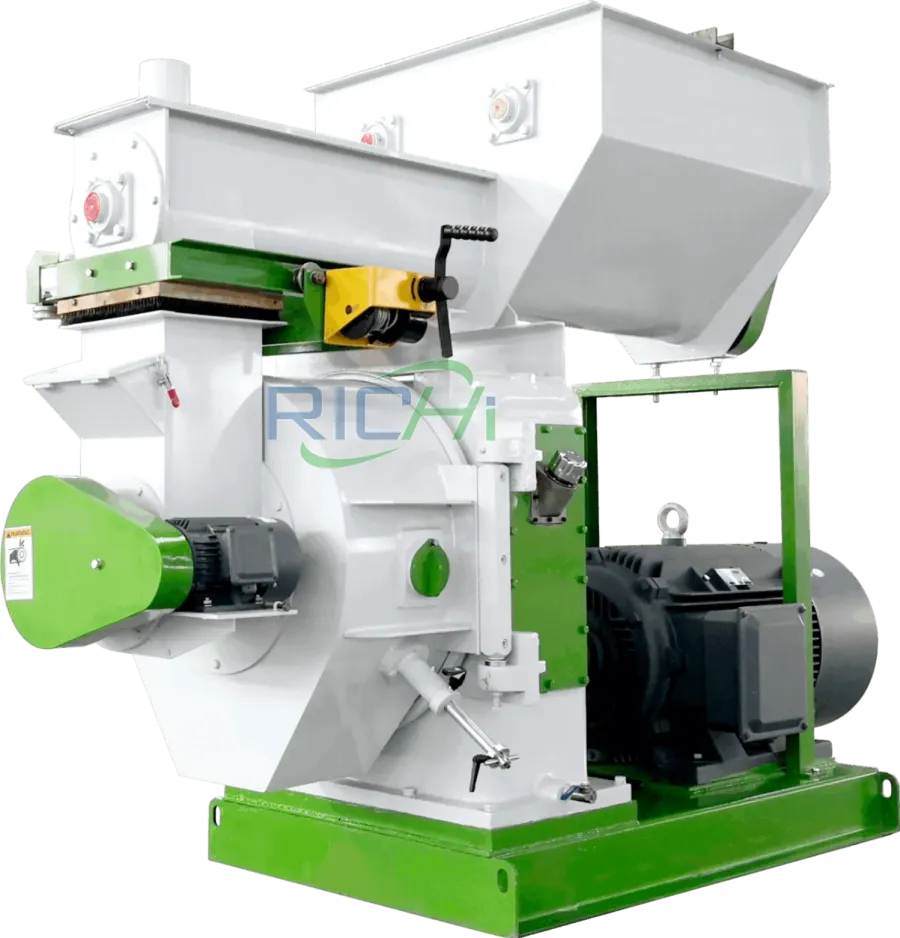
2. Challenges Posed by High – Moisture Raw Materials in Organic Fertilizer Pelletizers
2.1 Poor Granulation Quality
High – moisture raw materials are often too soft and sticky, making it difficult for them to form regular and stable granules in the pelletizer. In compression pelletizers, the soft and wet raw materials may not be able to withstand the compression force effectively, resulting in pellets with irregular shapes, low density, and poor strength. In extrusion pelletizers, the high – moisture content can cause the extruded materials to break or deform easily during the cutting process, leading to non – uniform pellet sizes. For example, when using fresh pig manure with a moisture content of over 70% in a compression pelletizer, the formed pellets may be flattened or crumbled due to insufficient hardness.
2.2 Equipment Clogging
The stickiness of high – moisture raw materials can cause them to adhere to the inner walls of the feed hopper, the channels of the extrusion part, and the surface of the rollers and dies in compression pelletizers. As the production progresses, the accumulated raw materials can gradually clog the equipment, disrupting the normal flow of materials and eventually halting the production process. In addition, the wet raw materials may also cause corrosion to some metal parts of the equipment, further reducing the service life of the pelletizer. For instance, in a disc pelletizer, high – moisture raw materials may stick to the disc surface, affecting the rotation of the disc and the agglomeration of the materials.
2.3 Low Production Efficiency
Due to the difficulties in granulation and the risk of equipment clogging, the production speed of Organic Fertilizer Pellet Machines when processing high – moisture raw materials often has to be reduced. Operators need to spend more time on equipment cleaning and maintenance to ensure its normal operation. Moreover, the need for additional pretreatment of high – moisture raw materials, such as drying, also adds to the overall production time. As a result, the production efficiency of the pelletizer is significantly lower compared to when processing low – moisture raw materials.
3. Pretreatment – Based Improvement Schemes
3.1 Drying
Natural Drying
Natural drying is a simple and cost – effective pretreatment method for high – moisture raw materials. This method involves spreading the raw materials in a large – area open space, such as a drying yard, and allowing them to be dried by sunlight and air circulation. For example, fresh manure can be spread in thin layers and turned over regularly to accelerate the evaporation of moisture. Natural drying is suitable for small – scale production or when the weather conditions are favorable. However, it has limitations, such as being highly dependent on weather, having a long drying time, and occupying a large area.
Mechanical Drying
Mechanical drying methods, such as using a rotary dryer or a fluid – bed dryer, can effectively reduce the moisture content of high – moisture raw materials in a shorter time. Rotary dryers use the rotation of a large cylinder to move the raw materials forward while hot air is blown through the cylinder to evaporate the moisture. Fluid – bed dryers, on the other hand, suspend the raw materials in a stream of hot gas, enabling rapid heat transfer and moisture evaporation. Although mechanical drying can improve production efficiency, it requires a certain investment in equipment and consumes energy, which increases the production cost.
3.2 Mixing with Dry Additives
Mixing high – moisture raw materials with dry additives is another effective pretreatment method. Dry additives, such as sawdust, straw powder, and peat, can absorb the excess moisture in the raw materials, improving their granulation properties. For example, when processing high – moisture poultry manure, adding an appropriate amount of sawdust can reduce the stickiness of the manure and make it easier to form granules. The ratio of dry additives to high – moisture raw materials needs to be carefully adjusted according to the moisture content and characteristics of the raw materials. However, adding too many dry additives may reduce the nutrient content of the final organic fertilizer product. (Related solution:Organic Fertilizer Production Line)
4. Equipment – Design – Based Improvement Schemes
4.1 Modifying the Feed System
Improving the Feed – Hopper Design
The feed hopper of the organic fertilizer pelletizer can be redesigned to better handle high – moisture raw materials. For example, a vibrating feed – hopper can be installed to prevent the raw materials from bridging or clogging in the hopper. The vibration can help the sticky raw materials flow smoothly into the pelletizer. In addition, the inner surface of the feed hopper can be coated with a non – stick material, such as polytetrafluoroethylene (PTFE), to reduce the adhesion of high – moisture raw materials.
Adjusting the Feed Rate Control
Precise control of the feed rate is crucial when dealing with high – moisture raw materials. A variable – frequency drive can be installed in the feed system to adjust the feed rate according to the actual processing capacity of the pelletizer. By monitoring the operation status of the pelletizer, such as the load of the main motor and the flow of materials in the extrusion part, the feed rate can be adjusted in real – time to prevent over – feeding and equipment clogging.
4.2 Optimizing the Granulation Chamber
Modifying the Structure of the Granulation Chamber in Compression Pelletizers
In compression pelletizers, the structure of the granulation chamber can be optimized. For example, the clearance between the rollers and the die can be adjusted to better adapt to high – moisture raw materials. A larger clearance can prevent the soft and wet raw materials from being over – compressed, reducing the risk of pellet deformation. In addition, the surface of the rollers and dies can be treated with special coatings or textures to improve the adhesion and compression effect on high – moisture raw materials.
Improving the Extrusion and Cutting Mechanisms in Extrusion Pelletizers
In extrusion pelletizers, the extrusion and cutting mechanisms need to be improved. The screw design can be optimized to enhance the conveying efficiency of high – moisture raw materials. For example, using a screw with a larger pitch at the feeding end and a smaller pitch at the extrusion end can better push the wet raw materials through the die. The cutting device can also be modified to ensure that the extruded materials are cut into uniform pellets. For instance, using a high – speed and sharp – edged cutting knife can improve the cutting quality of the soft and wet extruded materials.
5. Process – Control – Based Improvement Schemes
5.1 Adjusting Operation Parameters
Reducing the Rotation Speed
When processing high – moisture raw materials, reducing the rotation speed of the main components of the pelletizer, such as the rollers in compression pelletizers or the screw in extrusion pelletizers, can improve the granulation effect. A lower rotation speed allows the raw materials to be processed more evenly and gives them more time to form stable granules. However, the rotation speed should not be too low, as this may reduce the production efficiency. Therefore, an appropriate rotation speed needs to be determined through experiments according to the specific characteristics of the high – moisture raw materials.
Adjusting the Compression Pressure or Extrusion Force
In compression pelletizers, adjusting the compression pressure is crucial. For high – moisture raw materials, a lower compression pressure may be required initially to avoid over – compressing the soft materials. As the moisture content decreases during the granulation process, the compression pressure can be gradually increased. In extrusion pellet machines, adjusting the extrusion force can also affect the quality of the extruded pellets. By monitoring the extrusion process and the quality of the formed pellets, the extrusion force can be optimized to ensure stable production.
5.2 Adding Binders or Conditioners
Adding binders or conditioners to high – moisture raw materials can improve their granulation properties. Binders, such as starch – based binders, can enhance the cohesion of the raw materials, making it easier for them to form granules. Conditioners, such as lime or gypsum, can adjust the pH value and physical properties of the raw materials, reducing their stickiness. However, the type and amount of binders or conditioners added need to be carefully selected to ensure that they do not affect the nutrient content and environmental friendliness of the final organic fertilizer product.
6. Case Studies of Improvement Schemes
6.1 Case 1: A Small – Scale Organic Fertilizer Producer
A small – scale organic fertilizer producer mainly used fresh cattle manure as raw material, which had a high moisture content of about 65 – 70%. Initially, the producer faced severe problems with poor granulation and equipment clogging when using a compression pelletizer. After implementing a pretreatment method of mixing the cattle manure with sawdust at a ratio of 3:1 and reducing the rotation speed of the rollers in the pelletizer by about 20%, the granulation quality was significantly improved. The formed pellets had a more regular shape and higher density, and the equipment clogging problem was effectively alleviated. The production efficiency also increased by about 30% compared to before the improvement.
6.2 Case 2: A Medium – Sized Organic Fertilizer Plant
A medium – sized organic fertilizer plant used a combination of fresh poultry manure and food waste as raw materials, both of which had high moisture contents. The plant installed a rotary dryer to reduce the moisture content of the raw materials to about 40 – 45% before feeding them into the extrusion pelletizer. In addition, the plant optimized the screw design in the extrusion pelletizer and adjusted the cutting mechanism. After these improvements, the plant was able to produce high – quality organic fertilizer pellets continuously. The production capacity increased by 50%, and the quality of the pellets met the market standards, leading to an increase in market share.
7. Conclusion
In conclusion, dealing with high – moisture raw materials in organic fertilizer pelletizers requires a comprehensive approach that includes pretreatment, equipment – design improvement, and process – control adjustment. By implementing appropriate improvement schemes, such as drying, mixing with dry additives, modifying the feed system and granulation chamber, adjusting operation parameters, and adding binders or conditioners, the challenges of poor granulation, equipment clogging, and low production efficiency can be effectively addressed. Case studies have shown that these improvement schemes can significantly improve the performance of organic fertilizer pelletizers when processing high – moisture raw materials, promoting the development of the organic fertilizer production industry. In the future, with the continuous exploration and innovation in technology, more advanced improvement schemes for organic fertilizer pelletizers dealing with high – moisture raw materials are expected to emerge.